Write Us: info@rsainternationals.com
Quality Control in Apparel Production: Best Practices for Success
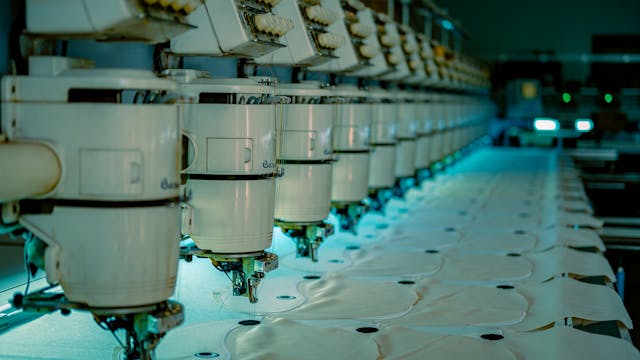
In this blog, we’ll explore the best practices for quality control in apparel production, providing you with the insights and tools necessary to achieve superior products and maintain customer satisfaction.
Why Quality Control is Crucial in Apparel Production
The apparel industry is complex, with multiple stages in the production process that can impact the final product. From fabric sourcing and cutting to stitching, finishing, and packaging, the potential for defects or inconsistencies is high. Without an effective quality control system in place, brands risk delivering products that don’t meet expectations, leading to increased returns, customer complaints, and damage to the brand’s reputation.
An effective quality control process ensures:
- Consistent Product Quality: Every garment meets the same high standard, leading to customer satisfaction and fewer returns.
- Cost Efficiency: Identifying defects early in the production process prevents costly mistakes that could result in wasted materials or rework.
- Brand Reputation: A commitment to quality enhances your brand’s reputation for reliability and excellence in the market.
- Compliance with Regulations: Meeting industry standards and certifications helps you stay compliant with local and international regulations.
Best Practices for Quality Control in Apparel Production
- Set Clear Quality Standards and Specifications
Before production begins, it’s crucial to establish clear quality standards and specifications. These should be aligned with the expectations of your target market, and agreed upon with your manufacturing partner.
- Material Standards: Ensure that fabric and trims meet quality benchmarks such as colorfastness, shrinkage, and durability.
- Design Specifications: Detailed technical packs, including measurements, stitching techniques, and finishings, help manufacturers understand and execute the design accurately.
- Functionality Requirements: For specialized apparel (e.g., activewear or outerwear), ensure that functional requirements like water resistance, breathability, and comfort are clearly communicated.
Setting these expectations up front ensures that the manufacturer has a clear understanding of what is required, reducing the chances of quality issues during production.
- Implement In-Process Quality Checks
Rather than waiting until the end of the production process to identify defects, it’s essential to implement quality checks at every stage of production. This proactive approach allows you to detect and address issues early, saving time and money.
- Fabric Inspection: Perform inspections when fabric rolls arrive to ensure there are no defects, stains, or issues that could affect the final product.
- Cutting and Sewing: Inspect the cutting and sewing processes to ensure patterns are followed precisely, seams are consistent, and no stitching issues exist.
- In-Process Sampling: Conduct random sampling of garments during different stages of production (e.g., after cutting, before stitching, and after finishing) to ensure they meet the quality standards.
In-process inspections help prevent the accumulation of defects that could affect the final product, ensuring a smoother workflow.
- Conduct Final Product Inspections
A final inspection is an essential part of the quality control process. This inspection should be thorough, evaluating the garment’s overall appearance, function, and durability.
- Visual Inspection: Check for defects such as loose threads, fabric damage, color inconsistencies, and incorrect labels.
- Measurements: Verify that the garment’s measurements match the specifications outlined in the design. A size deviation can cause problems for your customers.
- Functionality Tests: For garments with specific functionality (e.g., waterproof jackets or activewear), perform tests to ensure that these features perform as intended.
- Packaging: Ensure that the final packaging protects the garment during transit and that each product is properly labeled.
Final inspections should be done systematically with clear criteria, using trained and experienced inspectors. This stage ensures that only defect-free products are shipped to your customers.
- Use Quality Control Checklists and Documentation
Documenting quality control checks and processes is vital for maintaining consistency across production runs. Create detailed checklists for each inspection stage, outlining the specific aspects that need to be reviewed.
- Inspection Forms: These forms should include sections for inspectors to record their findings, including any defects or issues that were found.
- Tracking Defects: Use a defect tracking system to log any issues identified during inspections. This helps in monitoring recurring problems and addressing them with the manufacturer.
- Feedback Loops: Develop a system for giving constructive feedback to the manufacturer, helping them improve their processes and avoid similar issues in the future.
Documentation not only improves transparency but also helps track and analyze quality control performance over time, providing valuable insights for future production runs.
- Establish a Strong Communication System with Manufacturers
Quality control is not just about checking products at the end of production; it requires continuous collaboration between you and your manufacturer. Establish clear channels of communication to address any quality concerns in real time.
- Regular Updates: Set up regular meetings or reports from the manufacturer to update you on the status of production, any challenges, or quality concerns.
- Training and Support: Offer training sessions for the factory’s staff on quality standards and how to avoid common issues. Establish a feedback loop to help them understand what works and what needs improvement.
Good communication ensures that everyone is on the same page and that quality is prioritized at every step of the process.
- Conduct Random Inspections and Sampling
While regular inspections are important, random inspections of finished goods or in-process items add an extra layer of assurance. By inspecting a random sample, you get a better sense of the overall quality without checking every single item.
- Sampling Protocols: Implement random sampling protocols, where a percentage of the total order is inspected in detail.
- Third-Party Inspections: Use third-party quality control agencies, like RSA Internationals, to perform independent inspections of your products. Third-party inspections provide an unbiased evaluation of product quality and can help identify potential issues early.
Random inspections and third-party audits help ensure that the manufacturer maintains consistent quality standards.
- Focus on Continuous Improvement
Quality control should not be a one-time effort but a continuous process. Encourage manufacturers to implement continuous improvement initiatives that focus on reducing defects and enhancing product quality over time.
- Root Cause Analysis: When defects are identified, conduct a root cause analysis to determine the underlying issues and work with the manufacturer to address them.
- Quality Metrics: Use quality metrics (e.g., defect rates, rework rates, and customer returns) to assess performance and identify areas for improvement.
- Feedback and Innovation: Stay open to feedback from your manufacturers and customers. Use this input to innovate and refine your quality control processes continually.
A commitment to continuous improvement helps elevate quality over time, ensuring that your brand remains competitive and respected in the market.
Conclusion
Quality control in apparel production is an ongoing process that requires careful planning, consistent monitoring, and collaboration between manufacturers and brands. By implementing best practices such as setting clear quality standards, conducting in-process inspections, performing final product checks, and maintaining strong communication, apparel brands can ensure superior product quality and deliver exceptional value to their customers.
At RSA Internationals, we specialize in helping businesses streamline their quality control processes with comprehensive inspection services, factory audits, and expert guidance. With our expertise and support, you can confidently ensure that your products meet the highest standards and exceed customer expectations every time.
Really knowledgeable blog.
Thank you